There has been lots of post here recently about making wooden boards. How is it done, what wood to use, what are the measurements and various other questions. This is my attempt to answer some of these questions with a wooden board making tutorial. Mods if you like this tutorial, please make it a sticky thread. It may help redundant post in the future.
You can use almost any wood to make boards with. Basswood is preferred because it is clear (no knots) ,very soft and easy to work. However, most people do not have access to a good supply of basswood. Although not really ideal, plywood can be used. If you are using plywood take extra care to make sure that the edges are sanded very smooth so that they do not snag guard hairs of the fur putting it on and off. You can even use hardwoods although it would be a shame to waste good hardwood and driving tacks or nails in it would prove to be difficult.
I like pine. In my area of the country, it is easy to come by and if you go to the local mill it is cheap. The drawbacks are that it is knotty and sometimes it can have a lot of sap which you absolutely do not want on a stretching board. There are ways to overcome these obstacles. The easiest is cutting the knots out of the finished board and plugging it. If anyone does not understand this, perhaps I will add to this tutorial the next time I perform that task. As with any wood, make sure it is properly dry. Either by letting it sit for a period of time, buying kiln dried lumber or like I am doing in this tutorial, use recycled lumber. This particular lumber is recycled barn siding. It has been triple checked for any leftover nails before any machining was done. Make sure you do this. It will prevent dull and chipped blades. It is a safety factor also, you don’t need a nail flying out of a planer at 50mph!
I am an accomplished woodworker with a full shop. A lot of you will not have these tools. However, you may have a friend that does or you may use sized lumber and not really need all of these tools. This is a general tutorial of the steps I preformed using recycled lumber. Feel free to tweak them to suite your needs. The board I am making here is for a large coyote however, it is the same process for any board. I am shaping it to NAFA specs. You can download the NAFA fur handling manual here:
http://www.nafa.ca/wild-fur/resources I hope this helps everyone and also hope you enjoy.
Finally, on with the show:
1. The first thing I do is make a pattern out of ¼” plywood also know as sub flooring. I cut a strip to the widest point of the board and cut the strip to length. Mark a center line down the length of the board. Using your measurements that are in the NAFA handbook, lay out the appropriate distances and draw lines across. From your center line split all of the measurements in half and put a mark on each half of the centerline. After that has been completed, just connect the dots with a strait edge. Up at the nose, I just draw straight lines for reference and use a little poetic license to draw a nice rounded shape freehand.
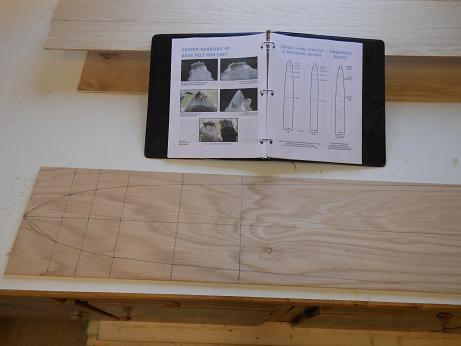
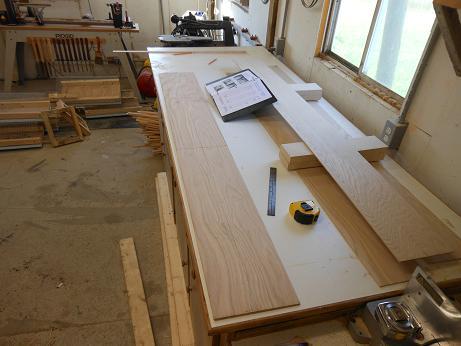
2. Cut this out on a table saw or use a jigsaw keeping the line visible. When cutting is complete, sand the edges to the lines giving the pattern a nice even flow. Now you have a pattern that you can use forever to make as many boards as you wish.
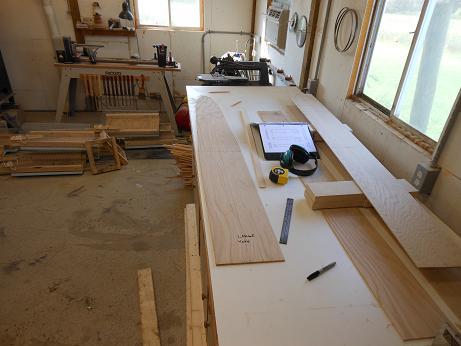
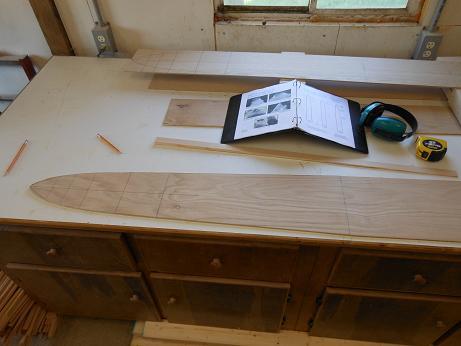
3. Here is my recycled barn siding. Yep, it is a little rough and horribly cupped. Normally, the way to get the cupping out is by machining one side on a jointer first. However, this is a very wide board. Much to wide for my jointer and to wide for most home shop jointers. A planer is the only way to really get most of the cupping out without getting really involved. The trick is to plane with the dome of the cup hitting the blades first. When one side is fully planed you can then flip it over. Take extremely shallow cuts here. The rollers on the planer will want to push the cup down during the feeding process and the board will just recup after the pass. Shallow cuts are the key. Below is also a picture of the first pass through the planer.
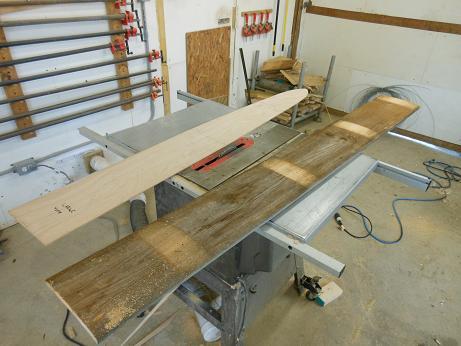
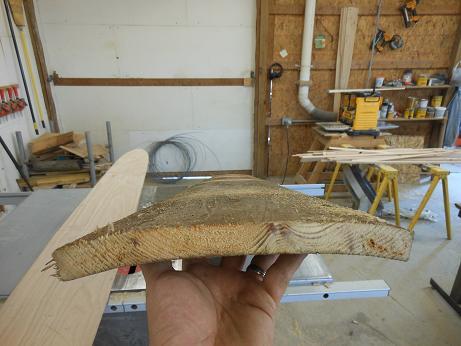
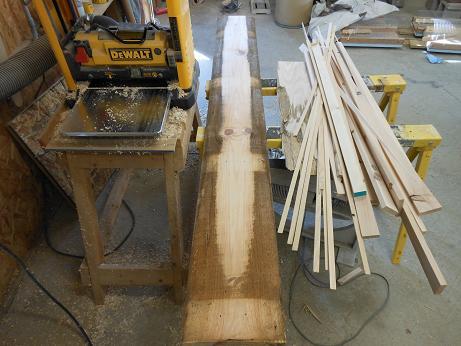
4. The board is now planed on both sides to a 5/8th thickness. As you can see 95% of the cupping is gone.
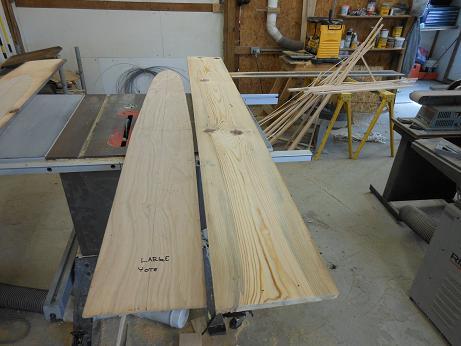
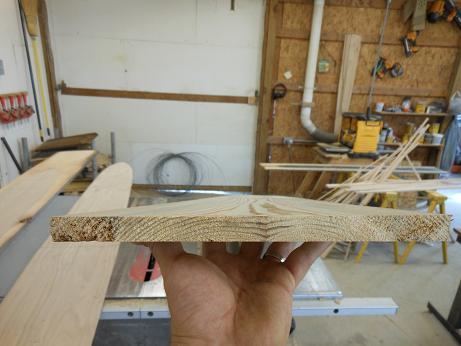
5. Placement of the pattern is next. If you are using a wood with knots, you want to make sure that the knots will be away from the edge of the board. You don’t want a knot popping out along the edge or it will have to be fixed because the fir will contour to the edge void when it dries and not want to release. Center your knots and Trace your pattern.
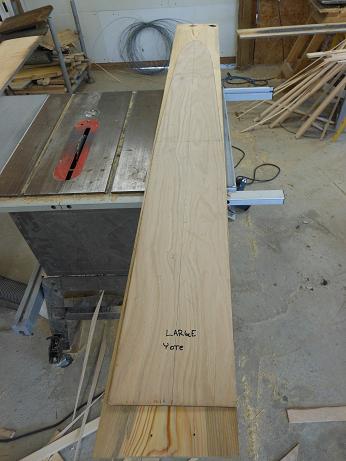
6. As with the pattern, you can cut out the stretcher with a table saw or jigsaw. Leave some space for sanding and after the board is cut out, sand the edges smooth up to your lines making a nice even flow to the board.

7. After sanding I use a router and give both sides of the board a rounded edge. This can be done freehand with your router if you don’t have a table. Set your router up on some of the scrap from cutting out the board. It would be a shame to cut to deep after all of this.
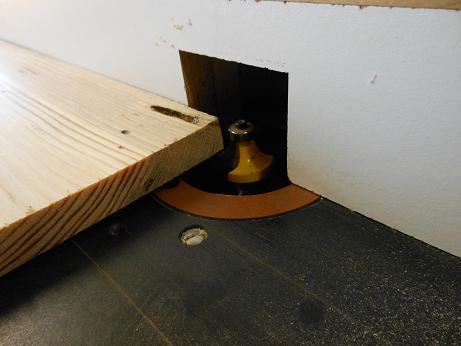
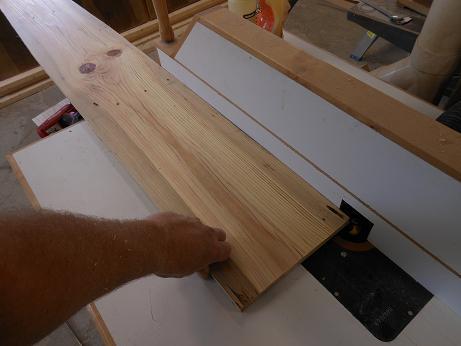
8. A final sanding. Sand the surface and smooth out any knots. Pay special attention to the edges. Sand them very smooth with a nice round to them. This will help the dried fur slide off and not pullout any guard hairs. Remember, if it’s rough on your finger, it to rough for fur.
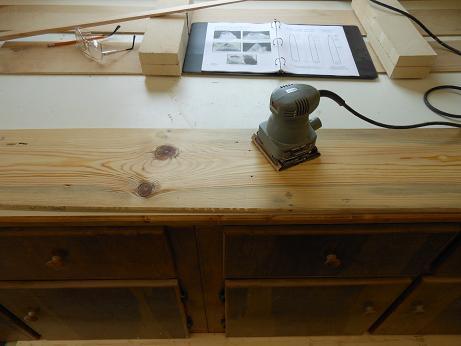
9. The final product, a large coyote board ready for fur. Hope you enjoyed this and it helps someone out.
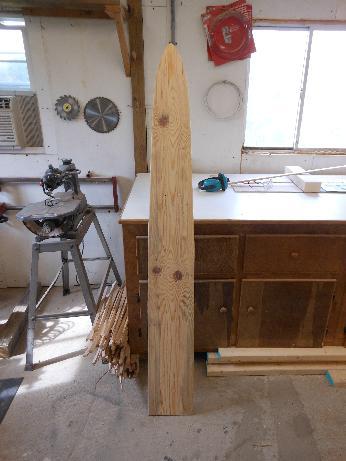